Een data afhankelijk voedselsysteem
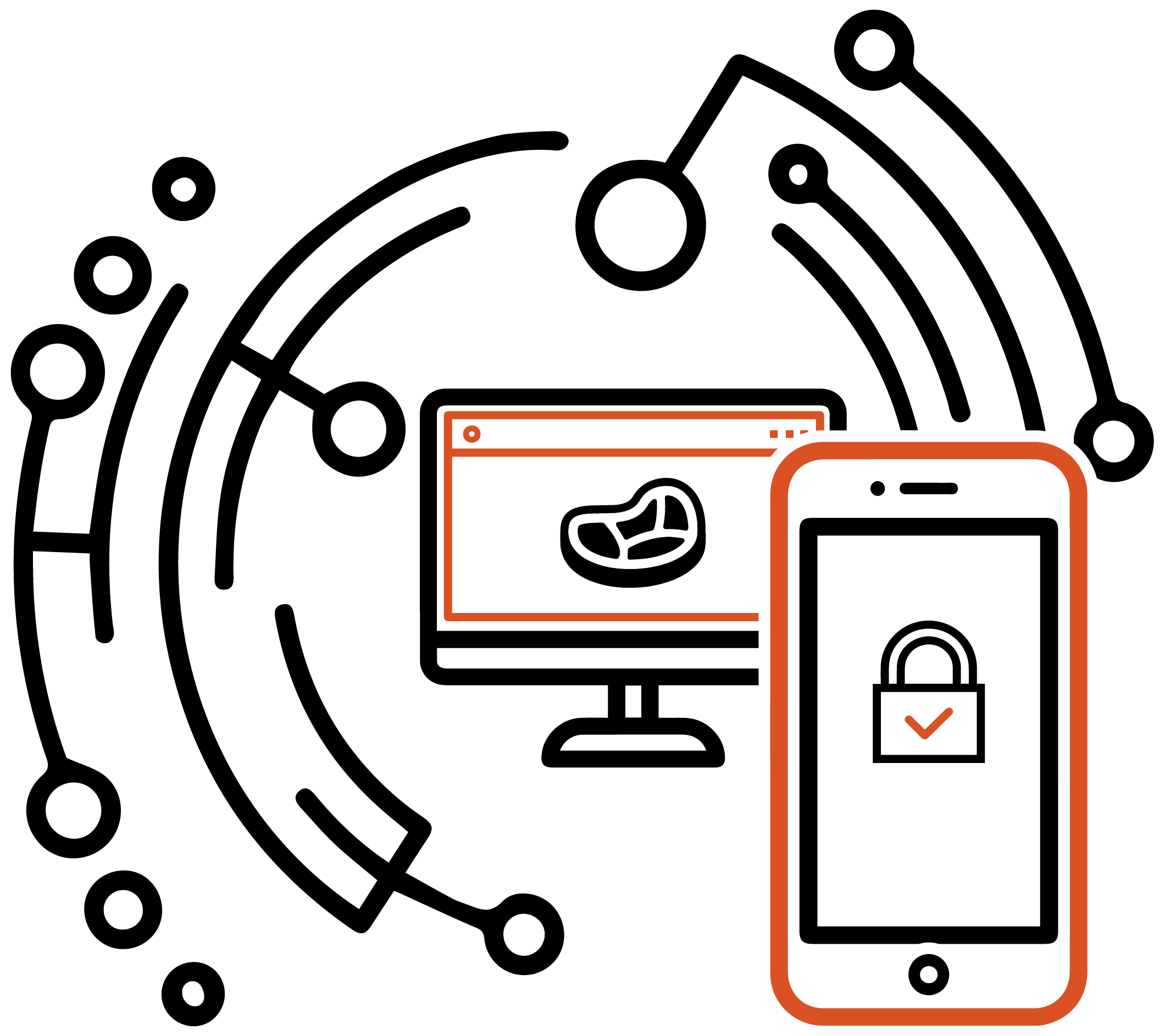
Smart data en veiligheid
Datatechnologie helpt voedingsproducenten om meer informatie uit de keten te delen. Voor de grote Nederlandse voedingsfabrikanten is de inzet van nieuwe technologieën niet alleen nuttig, het is ook noodzakelijk om concurrerend te blijven. Datatechnologie verhoogt de productiviteit van medewerkers en helpt om toekomstige personeelstekorten te voorkomen.
Richting 2030 gaan circa 40.000 van de 150.000 werknemers in de voedingsindustrie met pensioen. Als de sector zijn groei wil continueren, dan zijn aanvullend nog eens 7.000 extra mensen nodig. Door analyse van data is soms minder onderhoud van machines en installaties nodig. Systemen die gegevens over de status van productielijnen en de planning combineren, gaan medewerkers in de ‘control room’ van advies voorzien over de optimale aansturing van de verschillende productielijnen.
Bedrijven in de voedingsindustrie zetten slimme sensoren specifiek in voor het meten van producteigenschappen, zoals vochtgehalte, eiwitgehalte en droge stof. Die sensoren worden alsmaar kleiner, betrouwbaarder en goedkoper. Daardoor is het mogelijk ze vaker in het proces in te bouwen. Waar voorheen een operator een monster nam, analyseerde en daarop het proces bijstelde, zal de operator de komende jaren deze gegevens steeds vaker uitlezen van data voortkomend uit sensoren. Door artificial intelligence leren de systemen van eerdere situaties en worden adviezen beter. Betere metingen en dataverzameling in het veld (bij de boer/teler) maken de aanvoer vanuit toeleveranciers (o.a. over hoeveelheid en kwaliteit) veel beter te voorspellen. Op basis daarvan kunnen voedingsproducenten al eerder geschikte afnemers zoeken en een betere match tussen vraag en aanbod tot stand brengen. (UWV, 2019, ING Economisch Bureau, 2019 en Arink, 2020)
• WAT VERANDERT ER?
• TRACEERBAARHEID
Voedselveiligheid en transparantie worden steeds belangrijker. In de voedingsindustrie is de keten van producent naar consument steeds complexer en ondoorzichtiger geworden. Voedselschandalen in de keten hebben niet alleen het vertrouwen van de consument op de proef gesteld, maar ook dat van ketenpartijen in elkaar. Van de Nederlandse consumenten wil ruim de helft meer weten over de productie en herkomst van hun voeding en dan met name over vlees. Meer transparantie over de herkomst en productie van voeding helpt de afstand tussen producent en consument te overbruggen.
Datatechnologie faciliteert de uitwisseling van informatie in de keten, waardoor meer voedingsmiddelen tot op productniveau te traceren zijn. Door Radio Frequency IDentification-labels (RFID-labels) is het bijvoorbeeld mogelijk om vleesproducten van bron tot bord te volgen. RFID is een technologie om van een afstand informatie af te lezen van RFID-tags, -labels of -stickers. Via RFID-tags is het mogelijk de temperatuur van verzonden goederen te controleren. Daarvoor is vaak wel verregaande samenwerking binnen de productieketen nodig. Met behulp van datatechnologie, zoals blockchain, is de traceerbaarheid van producten voor de gehele keten naar 100 procent te krijgen. (ING Economisch Bureau, 2019)
Blockchain heeft veel potentieel in de voedingsindustrie. De toepassing is een kans om de impasse in de voedselketen te doorbreken. Centraal in de samenwerking binnen de blockchain staat het delen van data over het productieproces en de transacties die plaatsvinden binnen de keten. Het maakt het mogelijk om de verschillende ketens inzichtelijk te maken in een centrale database. Daarin kun je informatie vinden over voedselveiligheid, social compliance, kwaliteitsinformatie en milieu-informatie. Realtime is informatie te verkrijgen. Je kunt vooruitkijken: wat gebeurt er op dit moment met het product in de keten en voldoet het aan de voorwaarden van supplier compliance en productintegriteit? Alle partijen beschikken over dezelfde informatie en hebben inzicht in de transacties. Alle gebruikers krijgen bijvoorbeeld inzicht in de datum waarop een grondstof/product is geoogst, de temperatuur en de snelheid waarmee het zich heeft verplaatst en wanneer het product de fabriek heeft verlaten. Hierdoor wordt duidelijk zichtbaar hoeveel waarde elke schakel in de keten toevoegt en wat elke partij verdient. Met als resultaat een betere verdeling van marges. (VMT, 2018 en TNO, 2020)
In de voedingsindustrie bekijkt men of het mogelijk is de blockchain technologie op grote schaal in te zetten met verse productgroepen. Eind december 2020 heeft Vion in de Good Farming Star-varkensvleesketen de blockchaintechnologie geïmplementeerd. Blockchaintechnologie maakt de inspanningen van varkenshouders en andere ketenpartners bij de productie van varkensvlees zichtbaar. Door middel van JoinData, een coöperatie van bedrijven in de agrarische sector die de veiligheid van data-uitwisseling bevordert, kunnen alle ketenpartners op een veilige manier hun data delen. Via een machtigingenregister zijn de data van de ondernemer volledig geborgd. De ondernemer bepaalt zelf met wie hij of zij welke gegevens deelt. (Vion, 2020)
• GESLOTEN SYSTEMEN
Te verwachten is dat door het toenemende belang van veiligheid er steeds meer sprake zal zijn van gesloten systemen, beheerd door computers, sensoren en robots. Het product zal niet meer zichtbaar zijn, zodat er minder risico’s ontstaan tijdens het proces op bijvoorbeeld besmettingen. Kwaliteitsanalyses verschuiven steeds meer van het laboratorium naar de fabriek, waar digitale instrumenten de processen inline monitoren.
De foodsector zet sensortechnologie in voor pH-metingen, metingen van de kleur, omvang of het gewicht van producten en voor de aan- of afwezigheid van micro-organismen. (TNO, 2020) Door af te stappen van het papieren checklijstje dat de operator aan de lopende band moet afvinken en door meer inline te gaan meten, kunnen de verschillende processtappen en productcontroles beter geborgd worden. Flexibelere productie en de toename van het aantal kwaliteitsmetingen hebben uiteraard tot gevolg dat er veel meer data beschikbaar komen. Intelligente besturing maakt het realtime regelen van processen mogelijk. De voedselveiligheid en de kwaliteit zijn hierdoor beter gewaarborgd en het voedselverlies in de productie wordt verminderd. Datacollectie gaat nog veel belangrijker worden. Bedrijven kunnen wanneer ze data naar informatie omzetten veel meer en beter datagedreven beslissingen nemen. (Redactie VMT, 2020 en Redactie VMT, 2019)
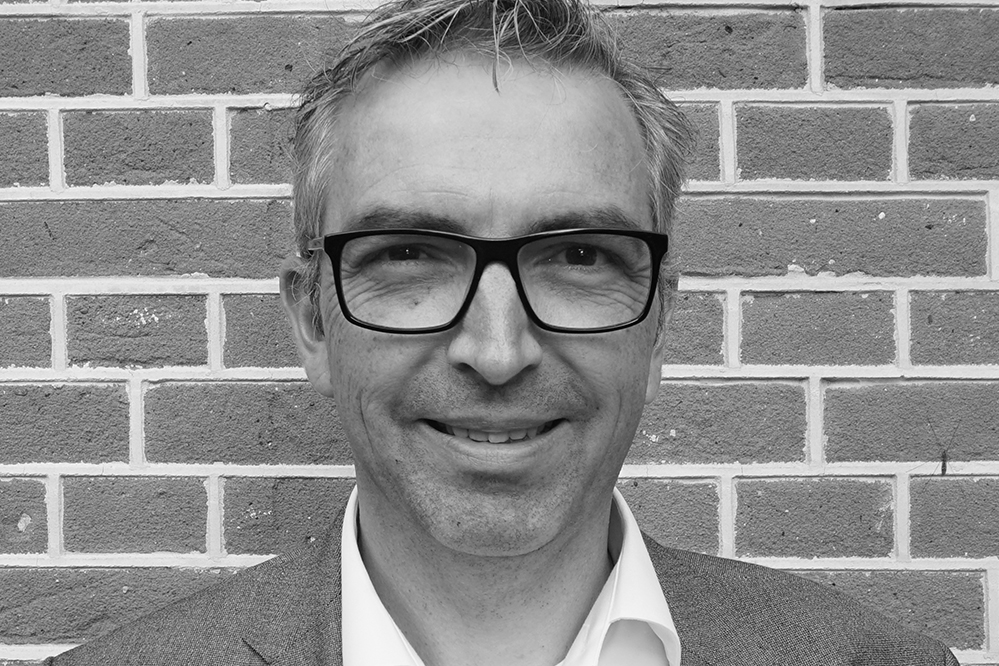
“Voedsel is nog nooit zo veilig geweest, toch is er wantrouwen vanuit de consument. Hetgeen in de keuken wordt gemaakt en op ambachtelijke wijze op de markt wordt gebracht vertrouwen mensen meer. De volgende stap daarin is transparantie. Je moet heel nauwkeurig werken, waar komt deze batch vandaan, wat gebeurt er? Het is zaak iedere handeling te registreren. De consument kan straks misschien wel een code scannen op bijvoorbeeld kaas en kan het hele productieproces bekijken.”
– Arry Verhage, SOL
• VACCP, HACCP EN TACCP
De werkwijze om productintegriteit te borgen, noemen we ook wel VACCP (Vulnerability Assessment and Critical Control Point System). Daarbij dient een bedrijf te controleren of ingekochte grondstoffen voldoen aan de eigen inkoopspecificaties en gestelde kwaliteitseisen. Naast deze controle ‘aan de ingang’ is het noodzakelijk om te controleren of zich geen risico’s voordoen tijdens het productieproces. In VACCP staan de volgende drie stappen centraal. Bij het verwerken van voedingsmiddelen kunnen er dingen misgaan, wat de veiligheid van ons eten in gevaar brengt. Bedrijven die voedsel produceren of verwerken, moeten mogelijke risico’s beschrijven in een voedselveiligheidsplan. Dit is een HACCP-plan.
HACCP staat voor Hazard Analysis and Critical Control Points. Een ‘hazard’ is een microbiologisch, chemisch of fysisch gevaar dat in een product aanwezig kan zijn en vervolgens een bedreiging voor de gezondheid van de consument kan vormen. Alle voedselverwerkers zijn verplicht een HACCP-plan op te stellen. Een goede hygiëne en voedselveiligheid zijn daarbij randvoorwaarden. Met HACCP loopt een bedrijf het hele productieproces na op mogelijke gevaren voor de veiligheid van voedsel en benoemt het bedrijf die gevaren. Vervolgens moeten bedrijven aangeven hoe ze de daaraan verbonden risico’s beheersen. Naast de risico’s rondom voedselveiligheid (onopzettelijke overtredingen) en productintegriteit (moedwillige fraude), is het ook mogelijk dat er veiligheidsrisico’s ontstaan door kwade opzet. Per 2021 wordt wel de vrijwillige HACCP certificatieschema voor voedselveiligheid vervangen door andere certificeringen, zoals de BRC Global Standard for Food Safety, IFC certificaat en de ISO 22000 certificering. Hierdoor komt er meer focus op het uitsluiten van risico’s door continue temperatuurbewaking.
De maatregelen die bedrijven hiertegen nemen, worden food defense genoemd met de TACCP-aanpak (Threat Assessment and Critical Control Point), vergelijkbaar met de werkwijze voor voedselveiligheid (HACCP) en productintegriteit (VACCP). TACCP focust zich daarbij op het voorkֶómen van opzettelijke besmetting van producten door kwaadwillende personen (inclusief eigen medewerkers). (FNLI z.d en Voedingscentrum, z.d.-b)
• PREDICTIVE MAINTENANCE
Bij predictive maintenance (voorspellend onderhoud) voeren bedrijven onderhoud niet te vroeg (preventief) of te laat (correctief) uit, maar op het juiste moment. Aan de hand van data kunnen ze voorspellen wat het meest geschikte moment voor onderhoud is. Een belangrijke reden om predictive maintenance in te voeren, is de uptime verbeteren. Eenvoudig is het echter niet om tot dit vrij abstracte niveau van onderhoud te komen. Doel bij predictive maintenance is dan ook om op het juiste moment de componenten te vervangen, net voordat het einde van de levensduur is bereikt. Zo verhoog je de beschikbaarheid en verlaag je de onderhoudskosten. De benodigde data zijn slijtage- of levensduurdata van de componenten die falen. Zo kun je nauwkeurig bepalen wat de exacte levensduur is en het bijbehorende uitvalpercentage. Als de kosten bekend zijn van zowel de reparaties (gepland en ongepland) als van de ‘downtime’, kun je tevens de optimale termijn bepalen voor het vervangen van de componenten. (Femto Engineering, 2018)
In de toekomst zal predictive maintenance een belangrijke rol gaan spelen in het verbeteren van de betrouwbaarheid van productielijnen en machines, doordat het storingen voorkomt en tegelijkertijd besparingen oplevert, omdat preventief onderhoud minder nodig is. Om de onderhoudsprocessen efficiënter te laten verlopen, maakt predictive maintenance gebruik van inlinesensoren, algoritmes en data-analyse. (TNO, 2020) Naast predictive maintenance is ook toezicht op afstand mogelijk, waarbij de taken van een monteur of operator veranderen.
• WELKE VOORBEELDEN ZIJN ER IN DE PRAKTIJK?
- Visproducent Princes gaat met behulp van blockchaintechnologie de consument inzicht geven in de reis van een blik tonijn. Met een QR-code en het nieuwe platform checkjevis.nl streeft Princes naar meer transparantie van de tonijnketen. Met een QR-code op de nieuwe verpakkingslijn kunnen consumenten de herkomst van de tonijn op een nieuw digitaal platform inzien. (Mooij, 2020)
- Machinebouwer voor de slachtindustrie Marel wil data delen tussen vleesverwerkers en supermarkten, zodat de consument kan zien waar het vlees vandaan komt. Dit kan middels de software in de machines van Marel, een grote speler in de slachttechniek. Dat leidt tot onderscheidende producten, voegt waarde toe en vergroot de bereidheid bij de consument om meer te betalen, zoals het geval is bij antibioticavrij vlees. Via keurmerken en QR-codes is het makkelijker om informatie over de samenstelling, herkomst en productie van voeding met consumenten te delen. De beperkingen van etiketten, zoals de beperkte ruimte en de nadruk op tekst, zijn daarmee deels op te lossen. Er is veel ruimte voor verbetering, want hoewel 85 procent van de consumenten etiketten leest, vindt bijna een derde de informatie onvoldoende. (ING Economisch Bureau, 2019 en Geesink-Stegeman, 2019)
• WAT IS DE IMPACT VAN SMART DATA EN VEILIGHEID OP HET WERKVELD?
• HET TYPE WERK VERSCHUIFT
Nieuwe datatechnologie is bepalend voor de toekomst van de werkgelegenheid in de Nederlandse voedings- en genotmiddelenindustrie. Mede vanwege het grote aandeel productiebanen staat een relatief groot deel van de werkgelegenheid bloot aan automatisering. Het heeft niet alleen invloed op de toekomstige hoeveelheid werk in de sector, maar ook impact op de aard van het werk. (ING Economisch Bureau, 2019)
Mensen zullen de grote hoeveelheid data moeten interpreteren om gerichte keuzes te maken. Slimme software en dashboards kunnen het omzetten van data in informatie ondersteunen. Het vertalen van data uit het productieproces naar kennis en nieuwe inzichten biedt nieuwe mogelijkheden, bijvoorbeeld voor het optimaliseren van productieprocessen. Daarnaast is het door de beschikking over data steeds gebruikelijker om predictief te werk te gaan. Bijvoorbeeld door te voorspellen welke consument op welk product zit te wachten. Gerichte marketing en gerichte R&D worden steeds belangrijker. (TNO, 2020)
Voor de sector is het belangrijk om personeel in staat te stellen om mee te groeien met deze ontwikkeling in kennis en vaardigheden. Medewerkers moeten zich constant blijven ontwikkelen. Competentieveroudering wordt een steeds grotere uitdaging, en duurzame inzetbaarheid en een leven lang leren worden steeds belangrijker. Om je te kunnen blijven ontwikkelen is niet alleen klassikale, formele scholing van belang, maar juist ook leren op de werkvloer. (TNO, 2020) Ook verwachten werkgevers vaker van medewerkers dat ze meedenken in het verbeteren van processen.
• BENODIGDE KENNIS
Om fouten te voorkomen is het nodig dat de medewerkers de gehele keten kunnen bedienen, beheersen en controleren. Zodat zij in staat zijn om het gehele proces te monitoren, van teelt tot levering aan de klant. Immers, door ketenbeheersing is een vers en volledig traceerbaar product te garanderen.
• BEHOEFTE AAN MEER TECHNISCH EN HOGER GESCHOOLD PERSONEEL
Door datatechnologie neemt de complexiteit van productieprocessen toe en dat noodzaakt tot het opwaarderen van bestaande banen. In de productie wordt mbo+ meer en meer de standaard. Terwijl inpak- en magazijnwerk automatiseert, stijgt de vraag naar productontwikkelaars, engineers en data-analisten. De behoefte aan hoger opgeleid en specialistisch personeel leidt tot meer concurrentie tussen de voedingsindustrie en andere sectoren. (ING Economisch Bureau, 2019)
Er is minder werk op mbo-niveau 2 en meer op mbo-niveau 3 en 4. De levensmiddelenindustrie heeft meer technisch en technologisch geschoold personeel nodig met een mbo- of hbo-diploma. Nu beschikken te weinig afgestudeerden over de juiste papieren. Negentig procent van alle mbo-functies wordt nog ingevuld door zij-instroom via de daarbij noodzakelijke bijscholing. (FNLI, 2015) Ook Arry Verhage (SOL) onderbouwt de behoefte aan hoger geschoold personeel: “Het werk van operators gaat meer naar niveau 3 en 4. Niveau 3 of 4 monitort het toezicht via een scherm. De operator op niveau 2 wordt steeds minder. Automatisering en sensoren nemen dat werk over. Dit heeft ook gevolgen voor de laborant. Minder monsters analyseren en vaker data analyseren.
• WERKZAAMHEDEN VERANDEREN
Operators krijgen met complexere technieken te maken. Eerst namen ze een aantal kwaliteitmonsters per dag, nu gaan ze naar een constant proces van 24 uursmonitoring. Steeds minder bepaalt de operator wanneer een productielijn start of wanneer ingrijpen nodig is. Daarentegen automatiseren bedrijven hun controlerende werkzaamheden steeds verder. Om productiestraten te controleren moet de operator een helder begrip hebben van de totale productielijn en op welke manier een softwaresysteem die lijn aanstuurt. Het werk wordt daarmee complexer en vereist waarschijnlijk minimaal een mbo-diploma op niveau 4.
“Als je kijkt naar het werken in de levensmiddelenindustrie deed je in het verleden als operator veel op basis van proeven, ruiken, horen. Nu verschuiven die functies steeds meer naar een beeldscherm. Handelingen worden geautomatiseerd door de introductie van sensoren. Je gaat deeg niet meer voelen, maar je gaat meten of het de goede samenstelling heeft. Het wordt steeds meer data aflezen en data analyseren. Wat je nu ook ziet, is dat het steeds meer gaat naar een continu productieproces; het product gaat erin en volgt allerlei processtappen. De ploegen zijn kleiner geworden. Toch zijn er niet minder mensen in de industrie gaan werken. De omzet en productie zijn omhooggegaan.”
– Arry Verhage, SOL
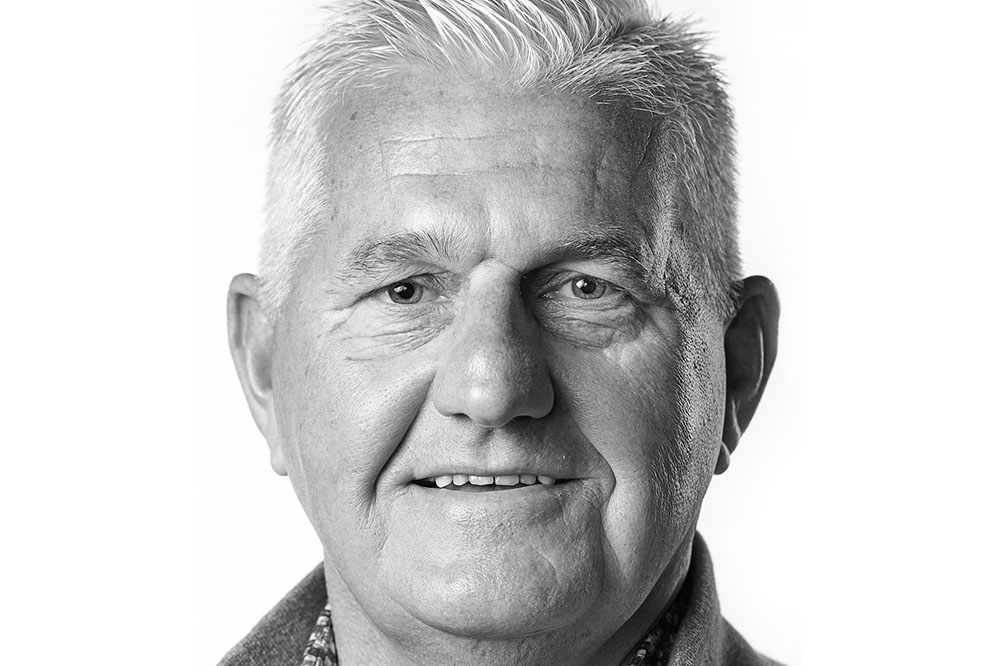
In de voedingsindustrie is steeds meer sprake van specialisatie. Automatisering en datatechnologie maken werkzaamheden specifieker: “Vroeger had je allroundbedrijven, maar die zijn zich gaan specialiseren. Allroundvakman dat bestaat bijna niet meer. Ga je in de keten kijken, van slachterij tot consumentenverkoop, dan is het helemaal uit elkaar getrokken en zijn er veel meer functies ontstaan. Operator, verkoopmedewerker, productiemedewerker etc.”
– Hans de Mooij, SVO vakopleiding food
Procesoperators krijgen in toenemende mate de verantwoordelijkheid voor de veiligheid van medewerkers in de fabriek en krijgen daarom taken op dat gebied toebedeeld. (TNO, 2020)
• BENODIGDE VAARDIGHEDEN
Verstand van de apparatuur die voor een steeds groter deel digitaal is, vraagt om digitale vaardigheden: digitale systemen kunnen instellen, maar ook gevoel hebben bij hoe die systemen werken. Dat betekent data, cijfers en rapportages interpreteren en dat kan met een bepaald denkniveau. Daarvoor moet je kunnen analyseren en visualiseren: dat op het moment dat een medewerker allerlei cijfers ziet, en een cijfer rood wordt, duidelijk is wat de operator moet doen. Hij moet in staat zijn om het proces te visualiseren: wat betekent het, wat is het effect ervan op het product en in de processen? Niet alleen moet de medewerker op die knop drukken als het cijfer rood wordt, maar hij moet ook (vak)kennis hebben van het proces, en weten hoe het zit, zonder het product aan te raken. Het werk heeft zich veel cognitiever en minder fysiek ontwikkeld.
Door de digitalisering komen steeds meer data ter beschikking en werken we steeds meer datagestuurd. Een storing wordt bijvoorbeeld aangeven op een display. De operator moet de informatie vervolgens kunnen duiden en er een actie aan verbinden. Ook kunnen we processen optimaliseren door analyse van de data. (TNO, 2020)
Het werk met datatechnologie vraagt van medewerkers een zekere mate van zelfstandigheid en nieuwsgierigheid. Ze moeten het leervermogen hebben om zelf op zoek te gaan naar informatie, en te bedenken hoe het proces beter en slimmer kan.
INHOUDSOPGAVE VOEDING
